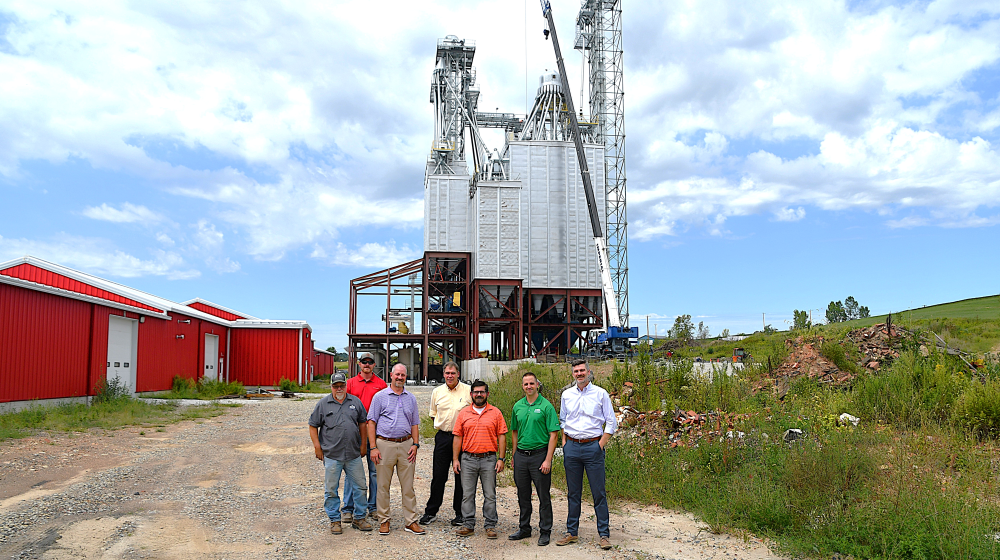
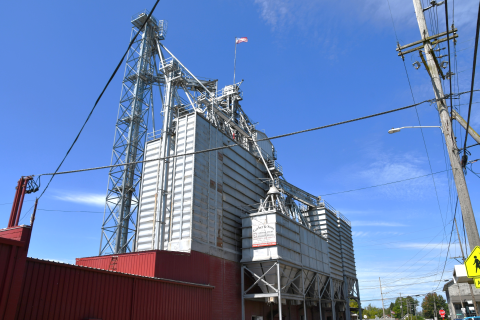
Towering over the main intersection of Baltic, Ohio, is the Gerber & Sons, Inc. feed mill. Since it first started in 1905, this family-owned business in rural Holmes County has produced custom feed mix and bulk feed for local livestock and poultry farmers.
The mill is complemented with four additional retail stores, a grain dryer, and a storage facility, all of which provide jobs for nearly 60 residents, some of whom have been “part of the Gerber family” for more than 40 years.
It still mixes, processes, and packages its product by hand without the benefit of modern automation, and teams of 14 employees work two 10-hour shifts daily to meet a demand that has grown to more than 2,300 farmers within a 100-mile radius of the mill.
“During our first full year of operation, the mill produced 23,000 tons of feed,” said Seth Gerber, the company’s president and general manager. “Now that same mill is producing more than 100,000 tons of feed per year.”
To keep pace with demand, Gerber & Sons knew it was time for a change. They needed a newer, more modernized mill that could manage the increased volume more efficiently.
So, they collaborated with Ohio’s USDA Rural Development team and a local banking partner, The Commercial & Savings Bank (CSB), to secure two loan guarantees through USDA’s Business and Industry Loan program.

"CSB has partnered with the USDA in the past, and we were thrilled to collaborate once again to help Gerber & Sons achieve their goal of modernizing the mill," said Clay Sinnett, a commercial loan officer with The Commercial & Savings Bank.
"As a community bank, supporting local businesses is at the heart of what we do," Clay continued. "This partnership with the USDA was essential to manage risk and ensure the project's success, which is vital for the prosperity of our local agricultural community.”
Through this lending partnership, Gerber & Sons, Inc., received a $20.5 million guaranteed loan to pay for construction and associated costs and a $4.5 million guaranteed loan to purchase new equipment to modernize the mill.
“Working with USDA has been a tremendous benefit,” Seth said. “They've helped us secure financing; they've helped us be able to purchase state-of-the-art equipment for our feed mill that will benefit the farmer and the customer so we can produce quality, consistent feed for our customers."
The new mill will have a building with automated equipment for processing and packaging, and a facility for grinding, mixing, and loading feed onto trucks for transport to customers.
“This project is about our employees, to make sure we have a solid family-owned company in the community,” said Seth. “We are also proud to work with family-owned farms in the area as our customers, and we want to make sure that this is around for another 100 years and more.”
The investments in building construction and equipment will help double the mill’s annual processing capacity of 1.65 million bushels of corn and will consolidate storage of more than 500,000 bushels of raw materials currently dispersed among five separate sites.
"Most importantly, this project is about our customers," Seth continued. "The customers we serve are still family-owned farms, generational farms, and we feel passionately about serving that community, and we absolutely feel this gives them a viable option for another 100 years for feed."
Construction is now underway; the new site is expected to open sometime in 2025.