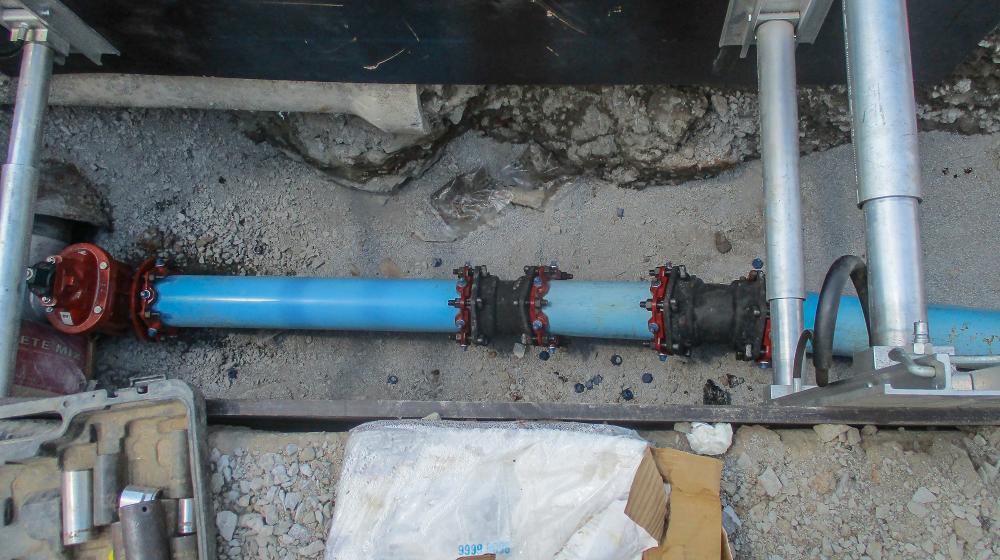
When Jeff Kilgore started work at the Woodway Water Authority (WWA), he found himself at the helm of a proverbial sinking ship with a small crew working feverishly to plug the leaks. The new executive director knew he had to drastically improve accountability to keep the operation sustainable and profitable.
“We were purchasing water from the towns of Jonesville and Pennington Gap and losing about 75 percent of it,” said Kilgore. “When you buy water, you just want to purchase what you need, and we weren’t being good stewards for our customers with that type of loss. Our whole goal was to fix any leaks we found, no matter how small they were.”
Kilgore started with a meter audit to get more accurate readings but encountered some roadblocks that made it nearly impossible to fully address the problems. His team didn’t have complete maps of line locations and the aging system he inherited didn’t have a lot of gate valves to contain the flow.
“We did much of the preliminary work in house, getting the meter readings every month to ensure they were working correctly and replaced dead meters,” said Kilgore. “Whatever it read, that’s what we billed with no averaging.
“We also split them into two zones, so we could pinpoint water losses on the Jonesville and Pennington sides. Then, we started tracking our pump stations to determine leak locations by kilowatts of electric consumption. If your kilowatts go up, that means your pumps are running more than they should and you have a leak in that zone.”
Though WWA was able to cut some of the losses through these measures, more needed to be done. Kilgore turned to the Lane Group to map out a systemwide project that included the replacement of more than 100,000 linear feet of water lines ranging from three-quarters to eight inches in diameter and installation of 96 gate valves and 64 fire hydrants. One of four water storage tanks would also be taken offline, and the water system reconfigured to ensure continuity of services.
“We found several areas in the Woodway water system that needed to be replaced,” said Project Manager Jon Broskey. “They had been aggressively working through the Virginia Department of Health to replace lines and complete smaller projects over the last 10 years, but this was a way to work on a larger scale to capture all the missing areas we were not able to touch.”
Gate valves were a critical addition to help WWA better isolate problems without knocking out the entire water system. Replacing nonfunctional fire hydrants was also key to providing adequate fire protection in the project area. Broskey says his group mapped out a plan to eliminate dead end lines and those with loops to improve fire flow in areas with different size lines.
When the team brought the proposal to Area Specialist Robert Hilt in USDA Rural Development’s Lebanon Office, he was able to help secure a loan and grant combination through the agency's Water and Environmental Programs that worked well for the authority. Timing also worked in their favor because Woodway was able to leverage pre-COVID pricing to get more work done than would have been possible six months later.
“We ended up with three total contracts and two different line contractors for this project,” said Broskey. “We completed the upgrades in a little over a year and were able to do some additional work because we got such great bid prices.”
During construction, Kilgore used in house GIS mapping capability to develop a more complete record of lines, gate valves and meters. Money saving measures also allowed the team to purchase leak loggers for use in pinpointing remaining problem areas and buy critical equipment like two new trucks and a set of red lights to better protect WWA employees in the field.
“We only have a three man crew here and can’t spare two of them as flaggers,” explained Kilgore. “If we are working in a high traffic area, we have to ask a nearby town for help. The portable lights can be set up on either end of the work zone and synced to control traffic and keep the workers safe.”
Water losses dropped from 75 to 13 percent after construction wrapped up this year, but Kilgore isn’t resting easy. With about 80 percent of the system upgraded, he is looking ahead to the next project so he can replace older lines in other parts of their system. Those steps will help WWA keep a tight rein on water purchases and rates and offer room for future growth.
“We made some changes to save us money and extend that benefit to our customers too,” said Kilgore. “Being proactive is key because you can easily go right back to that 75 percent figure if you don’t stay on top of things.
“I really appreciate Robert and USDA Rural Development. They were great to work with, and we now have extra capacity to offer services to areas that might need water but don't have it now due to this great team effort.”